“Building the perfect AR15 starts with the right materials and coatings.”
Types of Lower Receiver Materials
If you’re an AR15 enthusiast looking to build your own rifle, one of the most important decisions you’ll need to make is choosing the right lower receiver material. The lower receiver is the foundation of your rifle, so it’s crucial to select a material that is durable, reliable, and suits your needs. In this guide, we’ll explore the different types of lower receiver materials available, as well as the various coatings that can be applied to enhance their performance.
The most common materials used for AR15 lower receivers are aluminum, polymer, and steel. Aluminum is by far the most popular choice due to its lightweight, strength, and corrosion resistance. Most AR15 lower receivers are made from 7075-T6 aluminum, which is a high-strength alloy that provides excellent durability and reliability. Aluminum lower receivers are also easy to machine, making them a popular choice for DIY builders.
Polymer lower receivers are another option for AR15 builders looking for a lightweight and cost-effective alternative to aluminum. Polymer lower receivers are typically made from reinforced nylon or other synthetic materials, which offer good durability and impact resistance. While polymer lower receivers may not be as strong as aluminum, they are still a viable option for shooters looking to save weight without sacrificing performance.
Steel lower receivers are less common than aluminum or polymer, but they offer superior strength and durability. Steel lower receivers are often used in high-stress applications where maximum reliability is required. While steel lower receivers are heavier than aluminum or polymer, they are virtually indestructible and can withstand extreme conditions without failing.
When it comes to coatings, there are several options available to protect and enhance the performance of your lower receiver. Anodizing is the most common coating used on aluminum lower receivers, as it provides a hard, corrosion-resistant finish that is both durable and attractive. Anodized lower receivers are available in a variety of colors and can be customized to match your rifle’s aesthetic.
Cerakote is another popular coating option for AR15 lower receivers, as it offers superior durability and resistance to wear and tear. Cerakote is a ceramic-based coating that is applied in a thin layer to protect the surface of the lower receiver from scratches, abrasions, and corrosion. Cerakote is available in a wide range of colors and patterns, allowing you to customize your rifle to your liking.
For steel lower receivers, parkerizing is a common coating used to protect against rust and corrosion. Parkerizing is a chemical process that creates a protective layer of phosphate on the surface of the steel, providing excellent durability and resistance to wear. Parkerized lower receivers are often used in military and law enforcement applications where reliability is paramount.
In conclusion, choosing the right lower receiver material and coating is essential for building a reliable and durable AR15 rifle. Whether you opt for aluminum, polymer, or steel, selecting a material that suits your needs and preferences is key to a successful build. Additionally, applying a high-quality coating such as anodizing, Cerakote, or parkerizing can further enhance the performance and longevity of your lower receiver. By taking the time to research and select the best materials and coatings for your AR15 build, you can ensure that your rifle will perform flawlessly for years to come.
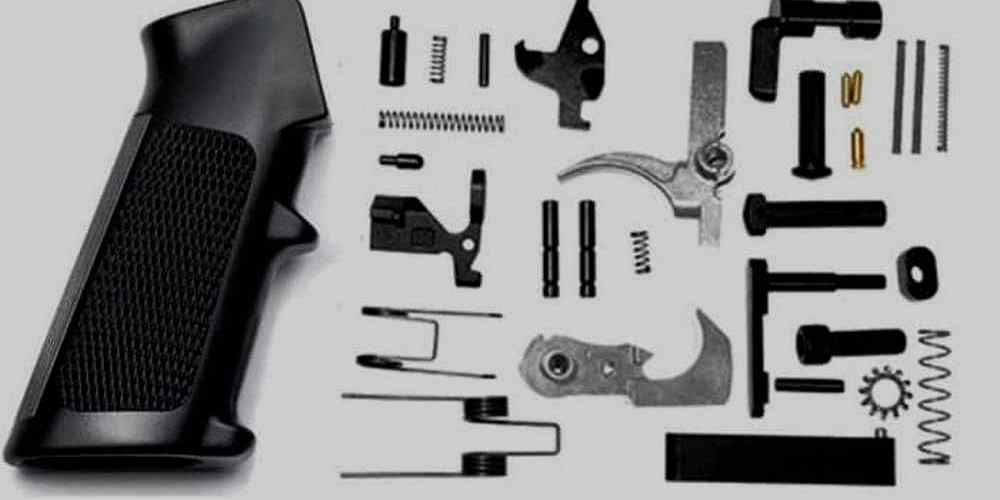
Benefits of Different Coatings for Lower Receivers
When it comes to building your own AR15, one of the most important decisions you’ll need to make is what materials and coatings to use for your lower receiver. The lower receiver is the foundation of your rifle, so it’s crucial to choose the right materials and coatings to ensure durability, reliability, and performance. In this guide, we’ll explore the benefits of different coatings for lower receivers to help you make an informed decision for your build.
One of the most popular coatings for AR15 lower receivers is anodizing. Anodizing is an electrochemical process that creates a protective oxide layer on the surface of the aluminum. This coating is known for its durability, corrosion resistance, and aesthetic appeal. Anodized lower receivers are available in a variety of colors, making it easy to customize the look of your rifle. Additionally, anodizing provides a smooth finish that is easy to clean and maintain.
Another popular coating option for AR15 lower receivers is Cerakote. Cerakote is a ceramic-based coating that offers superior durability, abrasion resistance, and chemical resistance. This coating is available in a wide range of colors and finishes, allowing you to create a unique and personalized look for your rifle. Cerakote is also known for its excellent adhesion properties, ensuring that your coating will stay in place even under extreme conditions.
For those looking for a budget-friendly option, a phosphate coating may be the way to go. Phosphate coatings are a type of chemical conversion coating that provides excellent corrosion resistance and wear resistance. While not as durable as anodizing or Cerakote, phosphate coatings are still a popular choice for budget-conscious builders. These coatings are typically black in color and provide a matte finish that is both functional and aesthetically pleasing.
If you’re looking for the ultimate in durability and performance, consider a DLC (Diamond-Like Carbon) coating for your AR15 lower receiver. DLC coatings are extremely hard, scratch-resistant, and provide excellent lubricity. These coatings are often used in high-performance applications where maximum durability and reliability are required. While DLC coatings may be more expensive than other options, they offer unmatched performance and longevity.
In addition to the benefits of different coatings for lower receivers, it’s also important to consider the material of the lower receiver itself. Lower receivers are typically made from either aluminum or polymer. Aluminum lower receivers are lightweight, durable, and offer excellent heat dissipation. They are also compatible with a wide range of accessories and upgrades. Polymer lower receivers, on the other hand, are lightweight, affordable, and resistant to corrosion. They may not be as durable as aluminum, but they are a popular choice for budget builds or lightweight setups.
In conclusion, choosing the right materials and coatings for your AR15 lower receiver is essential for building a reliable and high-performance rifle. Whether you opt for anodizing, Cerakote, phosphate, or DLC coatings, each option offers unique benefits in terms of durability, corrosion resistance, and aesthetics. Consider your budget, intended use, and personal preferences when selecting the best coating for your build. With the right materials and coatings, you can create a custom AR15 that is both functional and visually appealing.
Comparison of Aluminum vs Polymer Lower Receivers
If you’re an AR15 enthusiast looking to build your own rifle, one of the first decisions you’ll need to make is what material to choose for your lower receiver. The two most common options are aluminum and polymer, each with its own set of advantages and disadvantages. In this guide, we’ll compare the two materials to help you make an informed decision.
Aluminum lower receivers are the traditional choice for AR15 builds. They are known for their durability and strength, making them a popular option for those who prioritize reliability. Aluminum receivers are also more resistant to heat and wear, making them a good choice for high-volume shooters. Additionally, aluminum receivers can be easily customized with various coatings and finishes, allowing you to personalize your rifle to your liking.
On the other hand, polymer lower receivers are gaining popularity among AR15 builders for their lightweight and cost-effective nature. Polymer receivers are typically lighter than their aluminum counterparts, making them a good choice for those looking to reduce the overall weight of their rifle. Additionally, polymer receivers are often more affordable than aluminum receivers, making them a budget-friendly option for those looking to save money on their build.
When it comes to durability, aluminum receivers have the edge over polymer receivers. While polymer receivers are strong and reliable, they are generally not as durable as aluminum receivers. Aluminum receivers are less likely to crack or break under stress, making them a better choice for those who prioritize longevity and reliability in their build.
In terms of customization, aluminum receivers offer more options than polymer receivers. Aluminum receivers can be easily coated with various finishes, such as anodizing or Cerakote, to provide added protection and a personalized look. Polymer receivers, on the other hand, are limited in terms of customization options, as they are not as easily coated or finished as aluminum receivers.
When it comes to weight, polymer receivers have the advantage over aluminum receivers. Polymer receivers are typically lighter than aluminum receivers, making them a good choice for those looking to reduce the overall weight of their rifle. However, it’s important to note that the weight difference between the two materials is minimal and may not be a significant factor for most AR15 builders.
In conclusion, both aluminum and polymer lower receivers have their own set of advantages and disadvantages. Aluminum receivers are known for their durability and customization options, while polymer receivers are lightweight and cost-effective. Ultimately, the choice between the two materials will depend on your personal preferences and priorities for your AR15 build. Whichever material you choose, make sure to do your research and select a reputable manufacturer to ensure a high-quality lower receiver for your rifle.
How to Choose the Right Lower Receiver Material for Your AR15 Build
Building your own AR15 can be a rewarding and fulfilling experience. One of the most important decisions you’ll need to make when assembling your rifle is choosing the right lower receiver material. The lower receiver is the foundation of your AR15, so it’s crucial to select a material that meets your needs and preferences.
There are three main materials commonly used for AR15 lower receivers: aluminum, polymer, and steel. Each material has its own set of advantages and disadvantages, so it’s important to understand the differences before making your decision.
Aluminum is the most popular material for AR15 lower receivers due to its strength, durability, and lightweight properties. Most AR15 lower receivers are made from 7075-T6 aluminum, which is a high-strength alloy that provides excellent performance under various conditions. Aluminum lower receivers are also easy to machine and customize, making them a popular choice for builders who want to personalize their rifles.
Polymer lower receivers are another option for AR15 builders looking for a lightweight and cost-effective solution. Polymer lower receivers are typically made from reinforced nylon or other synthetic materials, which offer good durability and corrosion resistance. While polymer lower receivers may not be as strong as aluminum, they are still a reliable option for many shooters.
Steel lower receivers are less common than aluminum and polymer, but they offer superior strength and durability. Steel lower receivers are heavier than aluminum and polymer, but they are ideal for shooters who prioritize ruggedness and longevity. Steel lower receivers are also less prone to wear and tear, making them a popular choice for high-volume shooters.
When choosing the right lower receiver material for your AR15 build, consider your intended use and budget. If you’re building a lightweight and customizable rifle, aluminum may be the best option for you. If you’re looking for a budget-friendly and durable solution, polymer lower receivers may be the way to go. And if you prioritize strength and longevity, steel lower receivers are worth considering.
In addition to selecting the right material, you may also want to consider the coating or finish of your lower receiver. Coatings can provide additional protection against corrosion, wear, and scratches, while also enhancing the appearance of your rifle. Some popular coatings for AR15 lower receivers include anodizing, Cerakote, and nitride.
Anodizing is a common coating for aluminum lower receivers, which provides a durable and corrosion-resistant finish. Anodized lower receivers are available in a variety of colors and can be customized to match your preferences. Cerakote is another popular coating option, which offers superior durability and abrasion resistance. Cerakote lower receivers are available in a wide range of colors and patterns, allowing you to create a unique and personalized rifle.
Nitride coating is a durable and corrosion-resistant finish that is commonly used on steel lower receivers. Nitride-coated lower receivers are highly resistant to wear and tear, making them ideal for shooters who demand ruggedness and reliability. Nitride coating also provides a sleek and professional appearance, enhancing the overall look of your rifle.
In conclusion, choosing the right lower receiver material and coating is an important decision when building your AR15. Consider your intended use, budget, and preferences when selecting a material, and choose a coating that provides the protection and appearance you desire. With the right lower receiver material and coating, you can build a reliable and personalized AR15 that meets your needs and exceeds your expectations.
Tips for Proper Maintenance and Care of Lower Receiver Materials and Coatings
Building your own AR15 can be a rewarding experience, allowing you to customize your firearm to your exact specifications. One of the most important components of an AR15 build is the lower receiver, which serves as the foundation for the rest of the rifle. When choosing a lower receiver, it’s essential to consider the materials and coatings used, as they can impact the performance and durability of your firearm.
Lower receivers are typically made from either aluminum or polymer. Aluminum lower receivers are the most common choice among AR15 builders due to their strength and durability. They are also lightweight, making them ideal for a variety of shooting applications. Polymer lower receivers, on the other hand, are lighter and more affordable than aluminum receivers. However, they may not be as durable and may not withstand heavy use as well as aluminum receivers.
When it comes to coatings, there are several options available, each with its own set of benefits. Anodized aluminum is a popular choice for lower receivers, as it provides a hard, corrosion-resistant finish that is both durable and aesthetically pleasing. Cerakote is another popular coating option, known for its durability and resistance to wear and tear. It also comes in a wide range of colors, allowing you to customize the look of your firearm.
Regardless of the material and coating you choose for your lower receiver, proper maintenance and care are essential to ensure its longevity and performance. Regular cleaning and lubrication are key to preventing corrosion and wear on your lower receiver. When cleaning your lower receiver, be sure to use a solvent that is safe for the material and coating. Avoid harsh chemicals that can damage the finish and potentially compromise the integrity of the receiver.
In addition to regular cleaning, it’s important to inspect your lower receiver for any signs of wear or damage. Check for cracks, dents, or other abnormalities that could affect the performance of your firearm. If you notice any issues, it’s best to address them promptly to prevent further damage.
When storing your AR15, be sure to keep it in a dry, climate-controlled environment to prevent rust and corrosion. Consider investing in a gun safe or case to protect your firearm from dust, moisture, and other environmental factors that can damage the lower receiver.
If you plan on using your AR15 in harsh conditions, such as extreme heat or cold, consider applying a protective coating to your lower receiver. This can help prevent damage from exposure to the elements and extend the life of your firearm.
By choosing the right materials and coatings for your lower receiver and following proper maintenance and care practices, you can ensure that your AR15 performs reliably and lasts for years to come. Take the time to research your options and invest in quality components to build a firearm that meets your needs and exceeds your expectations. With the right knowledge and attention to detail, you can enjoy a custom AR15 that is both functional and durable.