“Secure your connections with precision and confidence.”
Importance of Proper Tightening Torque in Fasteners
When it comes to fastening components together, using the proper tightening torque is crucial for ensuring the integrity and longevity of the connection. Whether you are working with screws, bolts, or nuts, applying the correct amount of torque is essential to prevent loosening, stripping, or breakage of the fastener. In this article, we will explore the importance of proper tightening torque in fasteners and how it can impact the overall performance of your project.
One of the main reasons why proper tightening torque is important is to prevent over-tightening or under-tightening of fasteners. Over-tightening can lead to stress on the fastener, causing it to deform or break. On the other hand, under-tightening can result in the fastener coming loose over time, leading to potential safety hazards or damage to the components being fastened. By using the correct tightening torque, you can ensure that the fastener is securely in place without causing any unnecessary strain.
Another reason why proper tightening torque is crucial is to maintain the structural integrity of the components being fastened. When fasteners are not tightened to the correct torque, they may not be able to provide the necessary clamping force to hold the components together. This can result in gaps or misalignments between the parts, compromising the overall strength and stability of the assembly. By using the proper tightening torque, you can ensure that the components are securely fastened together, preventing any potential issues down the line.
In addition to preventing damage and maintaining structural integrity, using the correct tightening torque can also help improve the overall performance of the fastened components. When fasteners are tightened to the proper torque, they can distribute the load evenly across the joint, reducing the risk of fatigue or failure. This can result in a more reliable and durable connection that can withstand the demands of everyday use. By paying attention to the tightening torque of your fasteners, you can ensure that your project will perform as intended and last for years to come.
To determine the proper tightening torque for your fasteners, it is important to refer to the manufacturer’s specifications or guidelines. These guidelines will typically provide a recommended torque range based on the size and material of the fastener, as well as the type of components being fastened. Using a torque wrench or other torque measuring device can help you achieve the desired torque with precision and accuracy. It is also important to follow a proper tightening sequence, starting from the center and working your way outwards to ensure even distribution of the load.
In conclusion, proper tightening torque is essential for ensuring the reliability, safety, and performance of your fastened components. By using the correct torque, you can prevent damage, maintain structural integrity, and improve the overall performance of your project. Remember to always refer to the manufacturer’s specifications, use the right tools, and follow a proper tightening sequence to achieve the best results. With the right approach to tightening torque, you can ensure that your fasteners will hold strong and secure for years to come.
Common Mistakes When Tightening Screws and Bolts
When it comes to fastening components together, using screws and bolts is a common practice in various industries. However, one of the most common mistakes made when tightening screws and bolts is not applying the proper torque. Torque is the amount of force required to rotate an object around an axis, and it is crucial to ensure that screws and bolts are tightened to the correct torque specifications to prevent issues such as loosening, stripping, or breakage.
One of the most common mistakes people make when tightening screws and bolts is over-tightening. Over-tightening can lead to the stripping of threads, which can weaken the connection and make it more prone to failure. It can also cause the bolt or screw to break, especially if it is made of a brittle material. To avoid over-tightening, it is important to use a torque wrench and follow the manufacturer’s recommended torque specifications.
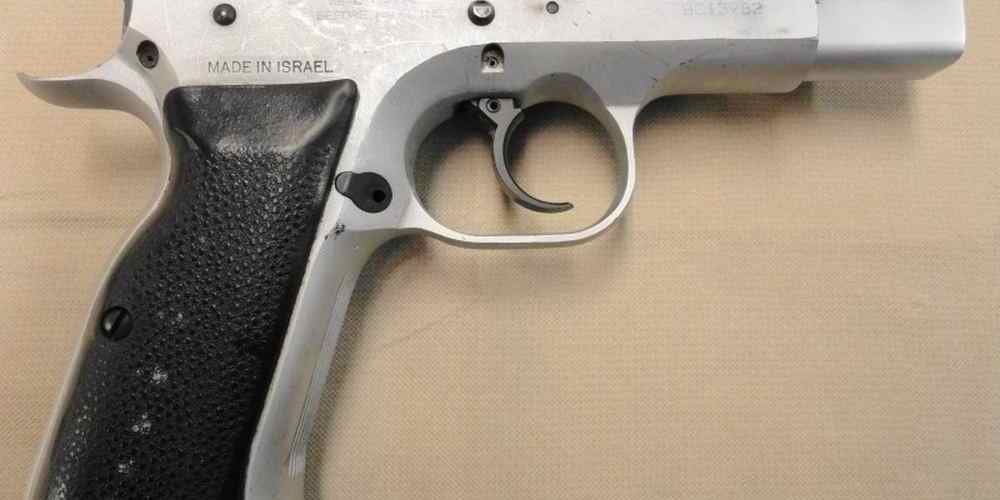
On the other hand, under-tightening screws and bolts can also be a problem. When screws and bolts are not tightened to the proper torque, they may come loose over time, leading to potential safety hazards. Under-tightening can also result in uneven distribution of load, which can cause components to shift or fail prematurely. To prevent under-tightening, it is important to use a torque wrench and apply the correct amount of torque as specified by the manufacturer.
Another common mistake when tightening screws and bolts is using the wrong tool. Using the wrong tool, such as a regular wrench instead of a torque wrench, can make it difficult to apply the correct amount of torque. This can result in over-tightening or under-tightening, both of which can lead to issues down the line. To ensure that screws and bolts are tightened properly, it is important to use the right tool for the job.
Additionally, not using the proper lubrication when tightening screws and bolts can also be a mistake. Lubrication helps reduce friction between the threads of the screw or bolt and the mating surface, making it easier to achieve the correct torque. Without lubrication, it can be more difficult to tighten screws and bolts properly, leading to potential issues with the connection. Using the right lubricant can help ensure that screws and bolts are tightened to the correct torque and prevent issues such as galling or seizing.
In conclusion, proper screw and bolt tightness is crucial to ensure the integrity and safety of connections in various applications. Common mistakes when tightening screws and bolts include over-tightening, under-tightening, using the wrong tool, and not using proper lubrication. To avoid these mistakes, it is important to use a torque wrench, follow manufacturer’s specifications, use the right tool for the job, and apply the proper lubrication. By taking these steps, you can ensure that screws and bolts are tightened correctly and prevent issues that can compromise the connection.
Tools and Techniques for Achieving Proper Tightening Torque
When it comes to working with screws and bolts, one of the most important factors to consider is the tightening torque. Properly tightening screws and bolts ensures that they are securely fastened and will not come loose over time. In this article, we will discuss the importance of tightening torque, how to achieve the correct torque, and the tools and techniques that can help you achieve proper screw and bolt tightness.
Tightening torque is the amount of force required to tighten a screw or bolt to a specific level. This level is typically determined by the manufacturer of the screw or bolt, and is important for ensuring that the fastener is securely fastened without being over-tightened. Over-tightening can lead to stripped threads, while under-tightening can result in the fastener coming loose.
To achieve the correct tightening torque, it is important to use the right tools and techniques. One of the most common tools used for tightening screws and bolts is a torque wrench. A torque wrench allows you to apply a specific amount of torque to a fastener, ensuring that it is tightened to the correct level. When using a torque wrench, it is important to follow the manufacturer’s instructions and to calibrate the wrench regularly to ensure accuracy.
In addition to using a torque wrench, there are other techniques that can help you achieve proper screw and bolt tightness. One technique is to use a threadlocker, which is a type of adhesive that helps to prevent screws and bolts from coming loose. Threadlockers are available in different strengths, so it is important to choose the right one for your application.
Another technique is to use a torque screwdriver, which is a screwdriver that applies a specific amount of torque to a screw. Torque screwdrivers are useful for applications where a torque wrench is not practical, such as when working in tight spaces or on small screws.
When tightening screws and bolts, it is also important to use the correct technique. One common mistake is to tighten screws and bolts in a circular pattern, which can lead to uneven tightening. Instead, it is best to tighten screws and bolts in a crisscross pattern, alternating between opposite sides to ensure even tightening.
In conclusion, proper screw and bolt tightness is essential for ensuring that fasteners are securely fastened and will not come loose over time. By using the right tools and techniques, such as torque wrenches, threadlockers, and torque screwdrivers, you can achieve the correct tightening torque and prevent issues such as stripped threads or loose fasteners. Remember to always follow the manufacturer’s instructions and to use the correct technique when tightening screws and bolts.
Effects of Incorrect Tightening Torque on Fastener Performance
When it comes to fastening components together, the proper tightening torque of screws and bolts is crucial for ensuring the integrity and performance of the joint. Incorrect tightening torque can have a range of negative effects on fastener performance, leading to issues such as loosening, stripping, or even failure of the joint.
One of the most common effects of incorrect tightening torque is loosening of the fastener. When a screw or bolt is not tightened to the correct torque, it may not be able to maintain the necessary clamping force to keep the joint secure. This can result in the fastener gradually working its way loose over time, leading to potential safety hazards and the need for frequent re-tightening.
In addition to loosening, incorrect tightening torque can also lead to stripping of the threads on the fastener or in the mating component. When a fastener is over-tightened, the excessive force can cause the threads to become damaged or stripped, making it difficult or impossible to properly secure the joint. This can result in the need for replacement of the fastener or even the entire component, adding unnecessary time and cost to the project.
Furthermore, incorrect tightening torque can also result in the failure of the joint altogether. If a fastener is not tightened to the correct torque, it may not be able to withstand the loads and stresses placed on the joint during operation. This can lead to catastrophic failure of the joint, potentially causing damage to equipment or injury to personnel.
To prevent these negative effects of incorrect tightening torque, it is important to follow proper tightening procedures when fastening components together. This includes using a torque wrench to ensure that the fastener is tightened to the manufacturer’s recommended torque specifications. It is also important to use the correct type and size of fastener for the application, as using an incorrect fastener can also lead to issues with tightening torque.
In addition to following proper tightening procedures, it is also important to regularly inspect fasteners for signs of loosening or damage. This can help to identify potential issues before they escalate into more serious problems, allowing for timely repairs or replacements to be made.
By understanding the effects of incorrect tightening torque on fastener performance and taking steps to prevent these issues, you can ensure the integrity and reliability of your joints. Proper tightening torque is essential for maintaining the safety and efficiency of your equipment, so be sure to always follow best practices when fastening components together.
Tips for Ensuring Consistent Tightening Torque Across Fasteners
When it comes to fastening components together, ensuring the proper tightening torque is crucial for maintaining the integrity and safety of the assembly. Whether you are working with screws or bolts, achieving consistent torque across all fasteners is essential to prevent loosening, stripping, or breakage. In this article, we will discuss some tips for ensuring consistent tightening torque across fasteners.
One of the most important factors in achieving consistent tightening torque is using the correct tools and equipment. A torque wrench is a specialized tool that allows you to apply a specific amount of torque to a fastener. By using a torque wrench, you can ensure that each fastener is tightened to the manufacturer’s specifications, preventing over-tightening or under-tightening.
Before using a torque wrench, it is important to calibrate it properly to ensure accurate torque readings. Most torque wrenches come with a calibration certificate that specifies the accuracy of the tool. If your torque wrench is not calibrated correctly, it may provide inaccurate torque readings, leading to improper fastener tightening.
When tightening fasteners, it is important to follow the manufacturer’s recommended torque specifications. These specifications are typically provided in the assembly instructions or technical data sheet for the component you are working with. By following these specifications, you can ensure that each fastener is tightened to the correct torque, preventing damage to the assembly.
In addition to using the correct tools and following manufacturer specifications, it is important to tighten fasteners in a consistent manner. This means applying the same amount of torque to each fastener in a sequence to ensure uniform tightness across the assembly. By tightening fasteners in a consistent manner, you can prevent uneven loading and stress on the components, reducing the risk of failure.
Another important factor in achieving consistent tightening torque is the use of lubricants on fasteners. Lubricants can help reduce friction between the fastener and the mating surface, allowing for more accurate torque readings. When using lubricants, it is important to use the correct type and amount specified by the manufacturer to prevent over-tightening.
When tightening fasteners, it is also important to consider the material and size of the fastener. Different materials and sizes require different torque specifications to achieve the proper tightness. For example, a larger bolt may require more torque to achieve the same level of tightness as a smaller bolt. By considering the material and size of the fastener, you can ensure that each fastener is tightened to the correct torque.
In conclusion, achieving consistent tightening torque across fasteners is essential for maintaining the integrity and safety of an assembly. By using the correct tools, following manufacturer specifications, tightening fasteners in a consistent manner, using lubricants, and considering the material and size of the fastener, you can ensure that each fastener is tightened to the proper torque. By taking these tips into consideration, you can prevent loosening, stripping, or breakage of fasteners, ensuring a secure and reliable assembly.