“Built to withstand the toughest conditions.”
Material Composition of AR15 Handguards
When it comes to the AR15 rifle, one of the most important components to consider is the handguard. The handguard plays a crucial role in protecting the shooter’s hands from the heat generated by the barrel, as well as providing a platform for mounting accessories such as lights, lasers, and grips. In order to perform these functions effectively, AR15 handguards need to be strong and durable. But what exactly makes a handguard strong and durable? Let’s take a closer look at the science behind AR15 handguard strength and durability.
One of the key factors that determine the strength and durability of an AR15 handguard is its material composition. AR15 handguards are typically made from either aluminum or polymer, with each material offering its own set of advantages and disadvantages.
Aluminum handguards are known for their strength and rigidity. Aluminum is a lightweight yet durable material that can withstand a great deal of abuse without bending or breaking. This makes aluminum handguards ideal for heavy-duty use, such as military or law enforcement applications. Additionally, aluminum handguards are able to dissipate heat more effectively than polymer handguards, which can help prevent overheating during extended shooting sessions.
On the other hand, polymer handguards are lighter and more affordable than aluminum handguards. Polymer is a synthetic material that is resistant to corrosion and can be molded into a variety of shapes and sizes. While polymer handguards may not be as strong as aluminum handguards, they are still capable of providing adequate protection for the shooter’s hands and accessories. Polymer handguards are also less likely to scratch or dent, making them a popular choice for recreational shooters and hunters.
In addition to material composition, the design of the handguard also plays a significant role in its strength and durability. Handguards with a free-floating design are generally considered to be stronger and more durable than handguards that are attached directly to the barrel. Free-floating handguards do not come into contact with the barrel, which helps to reduce heat transfer and minimize the risk of warping or bending. This design also allows for better accuracy and improved shooting performance.
Another important factor to consider when evaluating the strength and durability of an AR15 handguard is the method of attachment. Handguards that are securely attached to the rifle using a barrel nut or other mounting system are less likely to come loose or shift during use. Loose handguards can affect the accuracy of the rifle and pose a safety hazard to the shooter. It is important to choose a handguard that is properly installed and secured to the rifle to ensure reliable performance.
In conclusion, the strength and durability of an AR15 handguard are determined by a combination of factors, including material composition, design, and attachment method. Aluminum handguards offer superior strength and heat dissipation, while polymer handguards are lightweight and affordable. Free-floating handguards provide better accuracy and shooting performance, while securely attached handguards are less likely to come loose during use. By understanding the science behind AR15 handguard strength and durability, shooters can make informed decisions when selecting a handguard for their rifle.
Impact Testing and Durability of AR15 Handguards
The AR15 is a popular rifle platform known for its versatility and customization options. One key component of the AR15 is the handguard, which plays a crucial role in protecting the shooter’s hands from the heat generated by the barrel during firing. In addition to providing a comfortable grip, the handguard also serves as a mounting platform for accessories such as lights, lasers, and vertical grips.
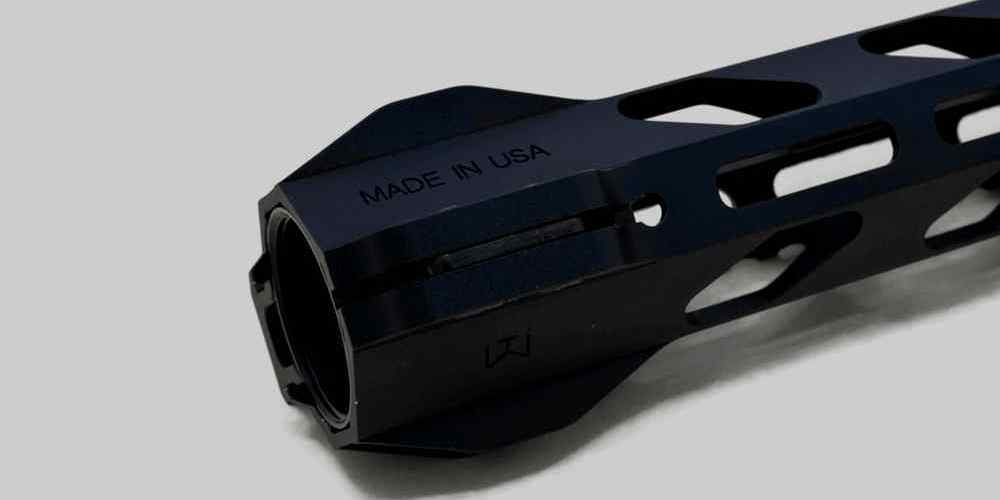
When it comes to choosing a handguard for your AR15, strength and durability are important factors to consider. A handguard that is not strong enough to withstand the rigors of shooting can fail, potentially causing injury to the shooter or damage to the rifle. To ensure that a handguard is up to the task, manufacturers subject their products to a series of impact tests.
Impact testing is a crucial step in determining the strength and durability of a handguard. During impact testing, a handguard is subjected to a series of controlled impacts to simulate the forces it may experience during use. This testing helps manufacturers identify weak points in the design and make improvements to ensure that the handguard can withstand the stresses of shooting.
There are several different types of impact tests that manufacturers use to evaluate the strength and durability of handguards. One common test is the drop test, in which a handguard is dropped from a specified height onto a hard surface. The handguard is then inspected for any signs of damage, such as cracks or fractures. Another test is the impact test, in which a weight is dropped onto the handguard to simulate the force of a bullet striking the rifle.
In addition to impact testing, manufacturers also conduct durability testing to ensure that a handguard can withstand repeated use over time. Durability testing involves subjecting a handguard to a series of cycles of heating and cooling, as well as exposure to harsh chemicals and environmental conditions. This testing helps manufacturers determine how well a handguard will hold up under real-world conditions.
One key factor that affects the strength and durability of a handguard is the material from which it is made. Handguards are typically made from aluminum, polymer, or carbon fiber. Each material has its own strengths and weaknesses when it comes to impact resistance and durability.
Aluminum handguards are known for their strength and durability, making them a popular choice among shooters who prioritize reliability. Polymer handguards are lightweight and affordable, but may not be as strong as aluminum handguards. Carbon fiber handguards are extremely lightweight and strong, but tend to be more expensive than other materials.
In conclusion, the strength and durability of an AR15 handguard are crucial factors to consider when choosing a handguard for your rifle. Impact testing and durability testing help manufacturers ensure that their handguards can withstand the rigors of shooting and provide reliable performance over time. By understanding the science behind AR15 handguard strength and durability, shooters can make informed decisions when selecting a handguard for their rifle.
Heat Resistance and Thermal Conductivity of AR15 Handguards
The AR15 is a popular rifle platform known for its versatility and customization options. One key component of the AR15 is the handguard, which plays a crucial role in protecting the shooter’s hands from the heat generated during firing. In this article, we will explore the science behind the strength and durability of AR15 handguards, focusing specifically on their heat resistance and thermal conductivity.
When it comes to heat resistance, AR15 handguards are designed to withstand high temperatures generated by repeated firing. The material used in the construction of the handguard plays a significant role in determining its heat resistance. Most AR15 handguards are made from aluminum, which is known for its excellent heat resistance properties. Aluminum can withstand high temperatures without deforming or losing its structural integrity, making it an ideal material for AR15 handguards.
In addition to heat resistance, thermal conductivity is another important factor to consider when evaluating the strength and durability of AR15 handguards. Thermal conductivity refers to the ability of a material to conduct heat. In the case of AR15 handguards, high thermal conductivity is desirable as it helps to dissipate heat away from the barrel and chamber, reducing the risk of overheating and potential damage to the rifle.
Aluminum, the most common material used in AR15 handguards, has a relatively high thermal conductivity, allowing it to efficiently transfer heat away from the barrel and chamber. This helps to keep the rifle cool during extended firing sessions, reducing the risk of malfunctions due to overheating. Additionally, the lightweight nature of aluminum helps to minimize the overall weight of the rifle, making it easier to handle and maneuver.
Another factor that contributes to the strength and durability of AR15 handguards is the design and construction of the handguard itself. Many AR15 handguards feature a free-floating design, which means that they are not attached directly to the barrel. This design helps to reduce the transfer of heat from the barrel to the handguard, further enhancing its heat resistance and thermal conductivity.
Furthermore, AR15 handguards are often equipped with heat shields or heat-resistant coatings to provide additional protection against high temperatures. These features help to insulate the handguard from the heat generated during firing, ensuring that the shooter’s hands remain comfortable and safe.
In conclusion, the strength and durability of AR15 handguards are crucial factors to consider when customizing your rifle. By choosing a handguard with high heat resistance and thermal conductivity, you can ensure that your rifle performs reliably and efficiently, even under the most demanding conditions. With the right materials, design, and construction, AR15 handguards can withstand high temperatures and provide optimal protection for the shooter’s hands.
Stress Analysis and Structural Integrity of AR15 Handguards
The AR15 is a popular rifle platform known for its versatility and customization options. One key component of the AR15 is the handguard, which plays a crucial role in protecting the shooter’s hands from the heat generated by the barrel during firing. In addition to providing a comfortable grip, the handguard also serves as a mounting platform for accessories such as lights, lasers, and vertical grips.
When it comes to choosing a handguard for your AR15, strength and durability are two important factors to consider. The handguard must be able to withstand the stress and forces generated during firing without deforming or failing. To ensure that a handguard meets these requirements, manufacturers conduct stress analysis and structural integrity testing.
Stress analysis involves evaluating how different forces and loads affect the handguard. This includes factors such as recoil, barrel harmonics, and the weight of accessories mounted on the handguard. By simulating these conditions, manufacturers can determine the maximum stress levels that the handguard will experience and design it accordingly.
Structural integrity testing involves subjecting the handguard to various tests to evaluate its strength and durability. These tests may include drop tests, impact tests, and endurance tests. Drop tests simulate the handguard being dropped onto a hard surface from a certain height to assess its ability to withstand impact forces. Impact tests involve striking the handguard with a blunt object to evaluate its resistance to sudden shocks. Endurance tests involve repeatedly mounting and dismounting accessories on the handguard to assess its long-term durability.
In addition to stress analysis and structural integrity testing, manufacturers also consider the material and construction of the handguard. Most AR15 handguards are made from aluminum, polymer, or carbon fiber. Aluminum handguards are lightweight and strong, making them a popular choice among shooters. Polymer handguards are also lightweight and durable, but may not be as strong as aluminum. Carbon fiber handguards are the lightest and strongest option, but also the most expensive.
The construction of the handguard also plays a role in its strength and durability. One-piece handguards are typically stronger than two-piece handguards, as they have fewer points of failure. Free-floating handguards, which do not make contact with the barrel, are also considered stronger and more accurate than traditional handguards.
When choosing a handguard for your AR15, it is important to consider your specific needs and preferences. If you plan on mounting heavy accessories such as bipods or grenade launchers, you may want to opt for a stronger handguard made from aluminum or carbon fiber. If weight is a concern, a polymer handguard may be a better choice.
In conclusion, the strength and durability of an AR15 handguard are crucial factors to consider when customizing your rifle. By conducting stress analysis, structural integrity testing, and considering the material and construction of the handguard, manufacturers ensure that their products meet the demands of shooters. Whether you are a competitive shooter, a hunter, or a recreational shooter, choosing a high-quality handguard will enhance the performance and longevity of your AR15.
Comparison of Different Handguard Designs for AR15s
When it comes to choosing a handguard for your AR15, strength and durability are two key factors to consider. The handguard is an essential component of your rifle, providing a mounting platform for accessories such as optics, lights, and grips. It also protects your hands from the heat generated by the barrel during firing. In this article, we will explore the science behind AR15 handguard strength and durability, and compare different handguard designs to help you make an informed decision.
One of the most important factors that determine the strength and durability of a handguard is the material it is made from. Aluminum is a popular choice for AR15 handguards due to its lightweight and durable properties. It is also resistant to corrosion, making it ideal for use in various environmental conditions. Another common material used in handguards is polymer, which is lightweight and affordable. However, polymer handguards may not be as strong as aluminum handguards and may not withstand heavy use as well.
The design of the handguard also plays a crucial role in its strength and durability. One-piece free-floating handguards are known for their strength and rigidity, as they do not come into contact with the barrel, allowing for consistent accuracy. They also provide a sleek and streamlined look to the rifle. Two-piece drop-in handguards, on the other hand, are easier to install and remove, but may not be as strong as free-floating handguards. They may also have more flex, which can affect accuracy.
M-LOK and KeyMod are two popular mounting systems used in AR15 handguards. M-LOK features a series of slots that allow for the attachment of accessories, while KeyMod uses keyhole-shaped mounting points. Both systems are lightweight and provide a low-profile mounting solution for accessories. However, M-LOK is considered to be more secure and versatile than KeyMod, as it allows for more flexibility in mounting options.
In terms of durability, handguards with a hard anodized finish are more resistant to scratches and wear compared to handguards with a standard finish. Anodizing is an electrochemical process that creates a protective layer on the surface of the aluminum, making it more durable and corrosion-resistant. Some handguards also feature a heat-resistant coating to protect the handguard from the heat generated by the barrel during firing.
When choosing a handguard for your AR15, it is essential to consider your specific needs and preferences. If you prioritize strength and rigidity, a free-floating handguard made from aluminum may be the best option for you. If you value ease of installation and removal, a two-piece drop-in handguard may be more suitable. Additionally, consider the mounting system and finish of the handguard to ensure it meets your requirements for durability and functionality.
In conclusion, the science behind AR15 handguard strength and durability is a complex and multifaceted topic. By understanding the materials, design, and features of different handguards, you can make an informed decision when choosing the right handguard for your AR15. Whether you prioritize strength, durability, or versatility, there is a handguard out there that will meet your needs and enhance the performance of your rifle.